A new mechanical weed control option has been added to Opico’s line-up, and is expected to appeal to a wide variety of users. David Williams was at the press launch.
Weed removal by hoeing was common practice until selective herbicides became available, but a reduced chemical armoury and increased chemical resistance, particularly in grass weeds such as black-grass, has renewed interest in the technique. Also creating additional demand for mechanical weed control are major buyers such as supermarkets, keen to supply food which has had less chemical exposure. For organic food production, which relies on mechanical and cultural weed control, hoeing remains essential to growing clean crops.
Mechanical hoeing provides many advantages over chemicals, but a disadvantage for large-scale farms has been the slower work rates needed to guide hoe bodies within just a few millimetres of growing crops. But, increased use of precision guidance and automatic steering has meant tractors can be relied upon to maintain an accurate track, so that mounted implements travel precisely. This has increased travel speeds, boosting work rates and increasing acceptability.
Opico offers a wide range of machinery through an excellent UK dealer network and adding a range of mechanical hoes to complement its current Comb Harrows will be popular with distributors and customers. Its new inter-row cultivators are manufactured by Austrian specialist Hatzenbichler, which has supplied harrows to Opico since 1994.
“The build quality is excellent,” explained Opico managing director, James Woolway. “There are several unique design features offering significant advantages for users.”
The Hatzenbichler family has farmed since the 1930s, and commenced implement manufacturing in 1952 when it produced its first mechanical weeder in the form of the Comb Harrow – the first of its type to enter production, and the predecessor to more than 7,000 units sold by Opico. A few years later it added inter-row cultivators to its range. The family switched to organic crop production on their farm in 1995 and the experience gained in finding solutions for their own crops contributes to product development.
Growing demand
“UK demand for Comb Harrows is mainly for organic farms,” explained James, “but we also supply them to some conventionally run farms and vegetable producers, particularly in recent years as supermarkets specify crops produced with fewer chemicals. We have seen growing interest in inter-row cultivation from all these sectors recently.
“We are also experiencing demand for mechanical weeding and inter-row crop establishment from maize growers, particularly where post-harvest soil run-off is an issue. This is certainly a market where interest will increase.”
James commented that potatoes are also a potential market for the technology due to the expectation that buyers will demand reduced chemical exposure in future, and he believes conventional arable crops will come under tighter scrutiny too, in terms of their environmental footprint.
Will it work?
Successful mechanical weed control depends on multiple factors, explained James, adding that it’s best to cultivate soil prior to crop establishment. Incorporating the technique into plough-based or min-till cultivation systems isn’t an issue, but it cannot be used in 100 per cent no-till establishment regimes unless crop residues are removed and the soil is easily worked.
Row widths have to be considered for inter-row cultivations and, while it is possible to mechanically weed between 12.5cm rows this might not allow the best weed control, depending on the crop and variety, if plants meet across the rows during the season. Wider row widths similar to those used in organic systems may become more popular as the inter-row technique is adopted on conventional farms. Weed emergence periods have to be considered in relation to weather conditions and crop development.
While inter-row cultivators tend to be used later in the growing season, comb weeders are used prior to establishment and through earlier stages of crop development. Stale seedbed combing is often used to remove weeds prior to drilling in the same way cultivation and chemicals are used. When weeding in the crop, multiple high speed passes of a comb harrow are used to control secondary weed growth resulting from seed germination encouraged by the first weeding pass.
The critical weed-free period for each crop – during which weed development could reduce yields – also needs consideration to make sure cultivation can provide control when needed.
James suggested that a hybrid system is attractive, combining mechanical with chemical weed control, offering advantages including reduced chemical reliance and lower production costs.
Opico is promoting both its Comb Harrow and inter-row cultivators as potential solutions for arable weed control.
Unlike the inter-row cultivators which cultivate aggressively between crop rows, the Comb Harrow is indiscriminate – raking across its full working width. Three gauges of rake steel are available, applying varying flexibility and working pressure. The thinnest 6mm is selected for vegetables and salad crops; 7mm is usually chosen for broad acre arable crops and 8mm, for the most aggressive raking, is used on grassland. The Hatzenbichler harrow has 30mm tine spacing and the raking action and sprung steel tines create the oscillation necessary to cover the entire surface.
A suitable tine angle is essential for optimum weed removal without crop damage, and Hatzenbichler comb harrows are supplied with manual or hydraulic rake angle adjustment in 10 stages. James stressed that this variation of pressure is needed, and to obtain best results it will typically be adjusted several times per day as the soil dries out or to suit different soil types.
Rakes are mounted in working sections which move and twist for accurate contour following. The main frame, along which the sections are mounted, is also capable of flexing to accommodate undulating field surfaces.
“The combing technique relies on crop roots being stronger than the weeds to withstand the raking action,” explained James. “As soon as the weed root is as big as the crop roots it’s too late, so subsequent passes to tackle new weed growth need to be while weeds are small. The Comb Harrow leaves a level surface and breaks up any capping, improving water infiltration and root zone air interchange. The raking action also stimulates tillering and releases surface nitrogen, so rather than damaging the crop, opportunities for higher yields are increased.”
Most Comb Harrows supplied by Opico are fitted with mounted seed/fertiliser applicators which make them very versatile. Demand for re-seeding grassland continues, but for arable farms the opportunity to cheaply establish cover crops is attractive.
Inter-row cultivators
The new inter-row cultivators accurately till between rows of growing crops to cut off the weeds just below the surface. They are fully adjustable and can be configured for any row width or combination of row widths. The line-up includes models from 2.5–18m working width to cultivate up to 72 rows in one pass. Front- or rear-mounted versions are available, along with trailed semi-mounted models, and although historically demand was for front-mounting for easier monitoring from the tractor seat, now rear-mounted are more popular as auto-steer systems require less operator input. Extra precision is also available through integral camera-controlled steering systems, mounted on the cultivator itself.
For automatic row following, Opico has teamed up with camera manufacturer Tillet & Hague, which develops and manufactures systems in the UK. Up to eight cameras can be mounted on each machine and the system combines the information provided and makes judgements regarding the optimum strategy, which is especially useful for complex headlands or where there are gaps in the crop. The cameras not only register the row position, but also calculate travel speed, so separate speed monitoring isn’t required. A minimum of two cameras are recommended, and the user can select which camera’s information should be used in advance, such as when approaching diagonal headlands.
Tillet & Hague’s software also allows for the addition of spot spraying technology on the cultivator.
The hoes mount on a guidance headstock from which the relative working position is varied by a double-acting, double-rod hydraulic cylinder. A potentiometer monitors movement to ensure precise positioning. Up to 250mm each side of centre is available, allowing accurate compensation for deviations caused by side-slopes, as well as errors due to drilling off-centre to the tramlines.
Moving the hoes sideways to follow plant rows creates powerful lateral forces. This is particularly the case with wider working widths, or when the tines are working deep. The tubular mounting frame is manufactured with a bespoke profile used by Hatzenbichler for more than 30 years. Each parallelogram unit clamps to the tube using a simple but positive mounting system which prevents unwanted movement, but allows easy adjustment of the mounting position for different row configurations.
If side forces exceed grip from the tractor’s rear wheels, then the tractor could be moved sideways leaving the hoe position unchanged and resulting in crop damage. To prevent this, Opico’s hoe has a pair of large diameter flanged steel wheels, which anchor the guidance headstock in line behind the tractor wheels for perfect row following.
Optimum results
The hoe carriers’ parallelogram mounting frames maintain pre-set working angles and pressure, while allowing accurate ground contour following. Different numbers of tines are fitted to the carriers, depending on row widths and crop types. For example; in cereals three rows are hoed per carrier with a minimum row spacing of 12.5cm.
All models fold for transport to under 3m and folded height is below 4m.
Vibro-tines with Duck’s foot shares penetrate hard dry ground, cutting weeds off below the surface without excessive soil movement.
Section control is an option expected to appeal to UK users. The Muller system provides automatic control of up to 13 sections which lift hydraulically as they reach the headland rows. This offers particular advantages for irregular fields where diagonal joints feature between the main field and headland. The biggest benefits are for wider working widths, where operation without section control would mean either missing triangular areas at the beginning or end of each bout, or destruction of some of the crop.
Tine options include S-tines or Vibro-tines fitted with either Duck’s foot or A-shares and, with endless adjustment available, almost any crops with adequate space between the rows can be tackled.
Adding a mounted applicator provides opportunities to apply nutrients precisely, or to under-sow or strip-seed additional crops through coulters or by broadcasting. “This is particularly beneficial where wide 75cm maize rows are used, as targeted application of fertiliser to the plant base avoids waste and reduces risk of run-off,” added James.
Further options include Kress finger weeders consisting of plastic-spoked discs operating at an inclined angle below plant foliage, and crop protection discs to reduce soil throw onto young plants.
Combined solution
Adding inter-row cultivators to Opico’s product offering is likely to prove a good move by the importer. The long-established relationship with Hatzenbichler means those investing in the products are assured of great back-up, including expert advice as to the best solution for their needs. Combining the benefits of a comb harrow and an inter-row cultivator makes sense, offering solutions for growing crops throughout the season, and additional options such as precision fertiliser placement and inter-row seeding adds possibilities for the future.
Prices for a 6m, 12-row inter-row cultivator suitable for sugar beet start at £19,851, and a 6m, eight-row version set up for maize is £21,458. A guidance headstock with a quick-hitching feature adds £28,405, and a seeder and platform adds a further £8,674.
Improved performance and new features of the latest Case IH Axial-Flow combines are expected to make it easier to establish and grow successful crops on a Romney Marsh farm. David Williams reports.
“We regard harvest as the first cultivation of the subsequent crop,” commented Andrew Cragg who trades as Brooker Farms based at Newchurch in Kent. “Getting that first cultivation right means subsequent operations are easier, and crop establishment is more even.”
Andrew farms approximately 565ha of his own crops including wheat, spring barley, oilseed rape and combine peas, and collaborates with a neighbouring farm, which means the combine can also harvest an additional area of similar crops as well as oats.
All straw is chopped and most crops are established by minimum tillage although ploughing is currently preferred for peas following spring barley, due to peas’ dislike of compaction and the amount of fluffy straw on the surface. Oilseed rape is established direct into stubbles which requires a fine chop from the straw chopper.
The farm was an early adopter of control traffic farming (CTF) and Andrew says this has contributed to an improved soil structure and reduced the need for deep cultivation.
Six years ago, the farm upgraded to a 12.5m (40ft) header, for compatibility with its planned 12–24m CTF regime from a previous 9m (30ft) model. “We wanted to make the most of opportunities offered by CTF and there were limited options for those looking for 12m machines. Several manufacturers offered the header width needed and were keen to help, but the standard unloading augers remained too short which meant corn trailers would have to travel off the tramlines,” explained Andrew. “When we asked about a longer auger at that time the response was generally negative as it was thought the additional weight would be too much for the lower pivot mounting, except for Case IH which agreed to produce us an extended version covered by the full factory warranty. So, we moved away from our previous brand, and bought our first Axial Flow combine from local dealer Ernest Doe Power.”
With the wider header and the amount of straw that had to be processed by the standard straw chopper, residue was sometimes inadequately spread resulting in blocking of cultivators and drills. Andrew discussed the issue with his dealer and Case IH, and a Europe-wide solution was identified in the form of a Canadian-manufactured Redekop MAV chopper which was fitted by Ernest Doe Power. The Redekop attaches to the rear of the combine behind the standard chopper. Special blades produce a powerful air blast which helps blow chopped straw and chaff out to the sides more consistently than the standard chopper. It worked well, providing the solution Andrew needed.
Power and automation
With the Axial Flow 9230 five years old and due for replacement earlier this year, Andrew had no hesitation in investing in the latest 9250 Axial Flow, boasting additional power (634hp max) and extra automation to improve performance and work rates. It also had a larger 14,500-litre grain tank. The extra-long unloading auger was now available as an option on the standard price list and a Redekop MAV Xtra-chopping chopper, now factory fitted, was also selected, based on the performance of the previous unit.
Additional technology on the new Axial Flow includes AFS Harvest Command automation. This uses a network of 16 sensors throughout the machine to monitor performance and, using the information generated, 7 different settings are automatically adjusted to optimise performance based on the selected harvesting strategy.
Three levels of automation include a base version, which simply makes initial settings, but Andrew’s 9250 model has the top AFS Harvest Command system. This includes Feedrate Control which adjusts ground speed based on crop load to meet a desired outcome – performance to control losses; maximum throughput, or fixed throughput. The operator selects maximum engine and travel speeds, and performance is optimised within these limits.
Andrew’s new combine also has a clean grain camera which identifies broken grains and impurities for grain quality monitoring, plus sieve pressure sensors to monitor the cleaning load. These sense impending overloads, allowing the cleaning system to operate at maximum capacity, while also making adjustments when needed to prevent losses before they occur.
Four operating strategies:
Performance – which maximises harvesting rate until grain losses from the rotor or cleaning system exceed pre-set parameters.
Fixed throughput – a target throughput is maintained by varying the travel speed while settings are adjusted to minimise losses.
Maximum throughput – the combine operates up to the speed or power limit set by the operator while adjusting settings to minimise grain losses.
Grain quality mode – settings constantly adjust to maintain targeted grain quality and impurity levels, while also minimising losses.
Auto feed-rate control
Darren said automatic travel speed control is selected most of the time, as it offers advantages in variable conditions, where speed increases in response to areas of thinner crop, and reduces where crop is thicker. During previous harvests he has suffered from shoulder pain after long days using the joystick to vary travel speed, but he said this wasn’t an issue this harvest and puts this down to the automatic speed management which reduces joystick use.
“I usually set the limit at 120 per cent of rated engine power, but aim to maintain a work flow using 100–110 per cent,” he said. “The speed control system is responsive and in patches of very thick crop, forward travel can stop abruptly while the threshing system deals with a sudden influx – but average working speed when crop flow is more even is approximately 5.5–7.0kph, which is quite comfortable with the 12.5m header. When filling a trailer alongside I always select manual speed control though, as sudden changes could cause problems for the trailer drivers.”
Optimise throughput
A new feature on the latest Axial Flow is rotor vane adjustment from the cab allowing the operator, or AFS Harvest Command in automatic mode, to adjust threshing performance for the crop and conditions. Adjusting the vanes to a shallow angle means crop remains in the rotor for longer for aggressive threshing, while a steeper angle moves the crop through more quickly, allowing higher work rates.
Sieve adjustment can also be adjusted manually, or automatically through AFS Harvest Command, in response to information from the loss sensors, grain camera and sieve pressure sensors.
“I’m very impressed with the sample from the new combine,” commented Darren. “The previous model allowed me to set the crop type, and settings were applied automatically after which I checked the sample throughout the day and made fine adjustments, but this does everything itself. I had my preferred settings written down for each crop harvested by the previous Axial Flow and it’s encouraging that the new combine makes almost identical settings in automatic mode. I try to maintain the best sample possible for all crops as that reduces the work load for the grain store. The new combine achieves a better sample whether I make the settings manually, or allow the combine to make them automatically and this year the oilseed rape was the cleanest we have ever seen.”
Higher work rates
Darren has driven combines for 16 years since being employed by Brooker Farms and at the time he joined the team, 2 combines were operated, later reducing to 1. “I like having the automation available as being able to rely on the combine to look after the settings leaves me free to concentrate on what is happening around me, especially when working in difficult conditions or at the headlands,” he explained. “The feature I like most is the automatic speed control. It lets me push the combine to full capacity when conditions are right to get as much harvested as possible without having to worry about overloading the rotor and blocking it. Even though this harvest was generally dry, during the early stages we had few really good harvesting days. Heavy dews held us up in the mornings and light rain showers forced us to stop in the afternoons, so making the most of harvesting opportunities as crops were ready was essential.”
Better chop quality
The new combine’s factory-fitted Redekop straw chopper is also performing well. Andrew said similar performance to the previous retro-fit model was expected, and he wasn’t disappointed. In very windy conditions where spread width can be compromised the fine chop means that cultivator and drill performance are unlikely to be affected.
The new 12.5m header has performed well this season in all crops and Darren said the optional in-cab controlled operating angle adjustment proved worthwhile, improving performance in laid barley to the extent that only two lifters at each end of the table were needed, rather than a full set.
The new Axial Flow has an improved transmission with field and road modes and on-the-move 2-speed range selection. The tracks are also improved with better suspension, and Darren said that at 30kph maximum travel speed the ride is more comfortable.
The latest cab is similar to before but noticeably quieter and Darren said he believes this might be due to the new tracks with their reduced vibration and smoother ride.
Daily maintenance requirements are minimal and Darren commented that the fuel and Adblue filling points are conveniently located.
Soils improving
Since moving to CTF, soil condition has improved and fewer cultivations are needed. “We no longer feel the need to make all the fields brown,” explained Andrew. “This year we have invested in a 12m Dale Drill for crop establishment direct into stubbles where possible, and with the improved performance of the latest Redekop chopper this shouldn’t present any problems. Oilseed rape will be drilled straight into the chopped straw. A 12m Lemken Heliodor cultivator will create a light tilth for winter wheat after peas and oilseed rape, and for spring barley after winter wheat. Next year we will also trial this approach for a small area of peas. Tramlines remain largely untouched while the wider combine tracks are remedied with a special 2-legged Flat-lift.
“We also have a set of 12m rolls so almost all our field operations are now 12m CTF compatible, and although our target is to minimise field work through direct drilling where possible, we will be flexible in our approach when conditions require.”
Easy decision
Andrew said that as a result of the farm’s experience with the previous Axial Flow combine, including back-up from the team at Ernest Doe Power, no other combine brand was considered this time. “The Axial Flow is simple and reliable and we achieve an excellent grain sample with minimal losses.
“The back-up is excellent and we have also had a visit from a delegation of US-based Case IH representatives to find out how we are getting on with the machine. They were interested in our feedback and keen to know what we need for the future.”
Combine key to success
Andrew says a result of moving to 12m CTF is that the machinery used is large for the area farmed, but allows field operations to be carried out when conditions are optimal. “The main motivation for moving to CTF has been to improve soil condition and we have seen that during the gradual transition the land has become gradually easier to work, requiring less deep cultivation. Our new 12m drill not only fits the farm’s standard working width but it will also allow us to make the most of opportunities to use minimum cultivations where conditions allow. However, the main component of the 12m traffic regime is the combine. The new Axial Flow 9250 has an ideal header size, an unloading auger which allows trailers to remain in the tramlines and a straw chopper which chops finely and spreads effectively, which is crucial for our progression towards minimal tillage.
“This is why I always regard harvesting as the first cultivation of next year’s crop.”
From the outside there isn’t a great lot different about New Holland’s latest T8 offering compared with previous models. But just a quick glance inside the cab makes it clear that the R&D team has been very busy. David Williams tried it out.
New Holland’s concept autonomous tractor did the rounds at UK shows a few years ago, with a futuristic cab incorporating bright-lit digital displays shouting about what tractors of the future might look like. Now the future is here and the ‘T8 Genesis with PLM Intelligence’ Horizon cab shares many characteristics with the experimental machine, including large, brightly coloured crystal clear displays that will appeal to operators.
The latest T8 line-up includes 5 models from 320–435hp (max EPM) and, like the previous range, the target market is larger arable farms and contractors, many of who will already be using precision farming technology to optimise efficiency of operations.
Most upgrades inside
From the outside, along with new decals, the most obvious indication that the tractor is the latest model is the lack of a B-pillar on the left side of the cab. Removing this has allowed a larger door for improved cab access.
Central locking is available using a new remote key which also incorporates a coded immobiliser. A master key can be programmed to access and start a whole fleet of the farm’s tractors while other operator keys can have access to different tractors allowed or denied.
The cab frame is similar to before, but a complete redesign resulting from user consultation includes extra storage for large items as well as odds and ends. The cab floor includes shaped compartments which prevent loose items rolling about.
With increasing use of electric-powered accessories there are a large number of 12-volt power points as well as USB-charging connectors. To the side of the driver’s seat in a large storage compartment, there is even a 240-volt socket likely to be popular with those who need to charge laptops during the working day.
With a nod to its American heritage the new T8 Genesis has leather upholstery similar to traditional American lorries or pick-ups, which is functional but extremely comfortable.
Heating and ventilation are upgraded with programmable zone control and additional vents.
Another update is improved semi-active cab suspension. Actuators under each side of the cab adjust the firmness of the ride while a large anti-roll torsion bar at the rear keeps the cab level.
Excellent visibility
Both rear view mirrors are on telescopic arms – allowing extension for use with high trailers and retraction to prevent damage when the extra length isn’t needed, using a switch in the cab. Front and rear cameras are standard and up to two additional cameras can be specified linked direct to the screen for implement or trailer monitoring. The front camera has a 170-degree field of vision, increasing safety for those emerging from fields on to a road through a hedge for example, where the view to the sides would otherwise be impaired.
For those working at night, 30 per cent extra lighting performance is available. New Holland T7, T8 and T9 product marketing manager for Europe, Darragh Mullin, talked Farmers Guide through the new model’s features and benefits, and he explained that the optional top specification 360-degree LED light package is currently the most popular lighting upgrade. However, an even more powerful 49,400-lumen light set for the new Genesis models is expected to prove even more popular.
Future potential
Traditionally New Holland has been closely aligned with Trimble for its display and guidance hardware but the new IntelliView 12 terminals for the T8 Genesis were designed in-house and use an Android operating system. This has given New Holland a free hand to incorporate any features it needs and, although the demonstration machine terminal included many new functions, developments continue and there is the potential for upgrades later – many of which remain secret for now.
Darragh explained that as use of precision farming technology increases, it’s likely that communication within a local network, including other machines in the field, will be the priority, while telematics for remote task monitoring and management will also be increasingly important. “Although full autonomous operation might be some way off yet, it’s likely that we will see linked machines working together much sooner, perhaps within just a few years. Examples would be a leader and follower situation for machines engaged in field work, or a tractor and trailer controlled automatically while a combine unloads.”
The amount of data required to allow ‘decisions’ to be made by the system in operations of this type is huge, and the new T8 has four Canbus networks rather than two on previous models. The main display is integral to the tractor and not intended to be swapped between machines, which suggests that New Holland sees it as the tractor’s brain rather than an accessory. With massive potential for upgrading in future, could these tractors be capable of fully autonomous operation as development of systems and legislation continues? Darragh didn’t agree or disagree but stated that it’s safe to assume the new T8 Genesis has the ‘building blocks’ for future autonomous operation if and when it becomes viable.
Operator friendly
A new SideWinder Ultra armrest is customisable, and divided into 3 areas with functions required 85 per cent of the time accessed through the Command Grip multi-function joystick. Those needed less often are adjacent on the main console and those used only 5 per cent of the time are in a strip further to the right. There are quick access buttons for 2 pre-set engine speeds, diff lock and 4wd, 5 configurable remotes which all incorporate easily-set locking functions, and up to 11 buttons which can be programmed with specific functions to suit user preference and applications.
A handy new feature making it easier to select and control hydraulic valve functions is the ability to configure and colour-code each switch to suit the task. The switches change colour to indicate the selected function and each can be configured for five function areas, with additional options available within each function menu.
The increased customisation, with many controls capable of multi-tasking, has resulted in 17 per cent fewer buttons and switches than previously, and the cab feels less cluttered than before.
All telephone controls are on the armrest, heat and ventilation settings are also conveniently to hand, and a new linkage control design in the form of a fixed computer ‘mouse’ for both front and rear linkages is also included. The mouse is palm-shaped with buttons and a scroll selector and allows all linkage functions to be controlled without the operator repositioning his hand.
To the right of the mouse is a smaller joystick which includes forward/reverse shuttle selector buttons, gear shift or range selector buttons as well as 2 configurable buttons.
The new Command Grip joystick design includes 20 per cent more buttons than before, and is now Isobus- and vehicle-configurable.
Isobus Class 3 is also available for the first time on T8 models allowing tractor control by implement and additional complex functions.
Obviously significant investment in hardware development has been made, and Darragh confirmed that, although the new T8-series have been selected as the first to have it, other tractors in the range will have it in future and it will also appear on New Holland machines such as harvesters.
A simplified form of the system through a retro-fit IntelliView 12 display will be available for other brands for maximum compatibility across a farm or contracting fleet.
Simpler hardware
Previous models had a separate GPS receiver, navigation controller and modem, but New Holland’s new GPS system is reduced to just two components making it simpler and easier to swap between machines.
New Holland claims an advantage of the new guidance hardware is that, because it is supplied and maintained through the New Holland main dealer, it’s easier to gain after-sales service and advice.
Increased compatibility with up to nine GPS satellite networks helps future-proof the system and will ensure accuracy in almost any location. N-Trip network compatibility provides accurate guidance by phone signal without a base station, but for those with RTK the new system is also fully compatible.
Maximum uptime
Meeting Stage 5 emissions regulations has been achieved through a larger catalyst chamber and without EGR or increased Adblue use. The fuel and Adblue tanks of the latest T8 are identical to its predecessor.
Servicing is every 600 hours as on previous models.
A handy new feature is self-calibration of auto-steer. All that is required is to set auto-calibration mode on the display, drive 100m in one direction and back again, and calibration is complete.
The latest track assemblies on SmartTrax half-track models have bolt-on rollers making replacement easier and the new rollers are also available to retro-fit to existing tractors. Rubber tracks are by Camso but New Holland is currently trialling Soucy tracks with a view to offering users an option.
Remote assistance services
New Holland Intelliview Connect is a service allowing the tractor operator to share his Intelliview display with a supervisor or dealer when requested, for assistance or problem solving.
Remote diagnostics allows the tractor’s systems to be checked for faults and, if the problem is caused by a setting error or software issue, there is the opportunity to correct it remotely at the time, or if parts are needed then the necessary component can be identified and an engineer can bring it for fitting, potentially saving a diagnostic visit. Remote firmware updates are also available wirelessly.
Maintenance requirements and fault notifications can also be monitored, allowing the dealer and user to schedule servicing and minimise downtime.
Practical test-drive
The flagship T8 Genesis 435 SmartTrax was working away from public view on a large Oxfordshire estate, with a Vaderstad Carrier cultivator on post-harvest cereal stubble which gave plenty of opportunity to try setting up and using the new control and guidance systems.
The in-house designed main IntelliView 12 terminal has working logic similar to a tablet and proved easy to use with simple menus accessed by touching the screen. Along the top of the display is an information bar with clear icons indicating which functions are selected and in use. The practical design doesn’t only include operation by screen touch which can be tricky on bumpy ground. Positive operation by quick-access buttons on the SideWinder Ultra armrest is just as easy to use and there is also control available through a twist dial with click selection.
Interactive
The new display is more interactive than anything seen before and the user can touch the screen to zoom in or out and even rotate the view.
A handy feature is the ability to record screenshots by pressing and holding the camera screen symbol. The images are stored and can be easily shared with others to highlight information of interest from performance data to guidance or Isobus-control images.
For task and machine management the user selects the task by description, then the attachment from a farm-specific drop-down list. Additional implements are easily added when needed. Full dimensions of the implement can be input and displayed for reference and an accurate diagram is shown.
When the operator chooses the task and implement from the menu, the guidance screen displays an image of the tractor and implement together – a clever feature which helps ensure the correct equipment and task have been selected for accurate record keeping.
The new IntelliView 12 display provides very easy set-up of guidance modes and working strategies which means that, with familiarity, just a few minutes is needed at the start of a task or a new field to create an efficient working pattern.
For simultaneous use of the screen for guidance while controlling and monitoring Isobus-compatible implements, the user has the option to select a split screen view.
New dashboard display
The previous A-pillar post display is replaced by Info View. This is a full colour display on the front console, providing essential tractor operating information including travel speed, engine revs, fuel level and temperature. Additional information such as cruise control speed settings are also available at a glance. As well as displaying operational information, a camera feed will also be available in future upgrades, with the digital screen reconfiguring to prioritise the camera image with all other information minimised and relocated.
Verdict
Although the new glowing displays look complex at first, it’s actually very easy to use the menus and work out how to check and change the main settings. The new control layout is excellent and everything is within easy reach. The colour-coded hydraulic controls make it easy to see at a glance which are needed and, if a different colour is preferred, then with a few touches of the screen the change can be made. The front instrument panel with its new Info View display provides most of the tractor performance information needed for the road and in the field and, because there is so much included, there is less need to refer to the main IntelliView 12 display, allowing the operator to keep his eyes to the front.
The new cab is easier to access through the wider opening door and, although the cab is the same size physically as its predecessor, it actually feels larger, mainly due to the revised instruments and control layout. Comfort is excellent and a run along a bumpy farm track emphasised the performance of the new cab suspension, although the luxury leather seats also played their part in the ride quality.
Brake to steer is new on SmartTrax models with customisable steering improving manoeuvrability and turning performance and reducing scuffing during turns.
Looking beyond all the clever functions available on the demonstration tractor, and mindful of the fact that many more remain in development for adding later, the new T8 Genesis PLM Intelligence series is likely to be an attractive long-term investment for professional farmers and contractors. It’s capable of so much more than cultivating stubble with an operator at the wheel and, in future – depending on legislation and industry acceptance, more of its capabilities will hopefully be revealed.
The T8 Genesis models will be unveiled officially at Agritechnica in early November and deliveries to customers will commence in late spring next year.
Brushcutters have a busy life on many UK farms and estates playing a vital part in keeping grass and weed growth under control. Sales of battery-powered models are increasing and Farmers Guide arranged an on-farm test of a petrol model and an equivalent electric version to see how they compared. David Williams reports.
Not long ago battery-powered strimmers were considered a novelty and a last resort for professional users, often selected only when lower operating noise was essential or for domestic users where storing petrol was an issue. Now, in common with other electric tools, improved battery power, capacity, and extended working times have made them a practical alternative and agricultural dealers report that a gradual changeover from petrol to electric powered models is in progress.
Farmers Guide asked Stihl to supply its most popular petrol model for farm tasks, along with an equivalent battery-powered model to compare, and lent both for a three-week test with Euston Estate on the Norfolk-Suffolk border.
Euston Estate is home to the 12th Duke of Grafton and his family and, along with extensive parkland as well as 28ha of gardens, there is a large farming enterprise including woodland, stewardship grassland, arable crops and a vegetable enterprise run in conjunction with RG Abrey Farms. There is an award-winning solar energy installation and an anaerobic digester for which maize is grown. Livestock include cattle, horses, pigs, sheep and poultry and with all the enterprises across more than 4,300ha there is plenty of work for the maintenance and groundcare team.
The brushcutters recommended by Stihl were FS111 petrol, and FSA130 battery models.
Ideal test user
Jamie Fairs is a member of Euston’s gardening and maintenance team and is well used to working with a variety of brushcutters. As well as keeping paths and tracks clear of grass and brambles, and trimming areas which can’t be reached by tractor-mounted mower, his work includes maintaining verges and other grass areas around Euston village.
“I was very open-minded about the battery-powered version,” he explained. “Stihl is a respected manufacturer and I was quite confident that the electric model would be capable of professional use, but to what extent it could compete with a petrol machine I wasn’t so sure. I was fairly certain the battery model would be nicer to use with less noise and vibration.”
The FS111 petrol model was equipped with a Stihl AutoCut head which holds a reel of nylon line and automatically feeds out a set length each time the release button is knocked on the floor.
The FSA130 had a Stihl PolyCut head designed for trimming larger areas and which has three solid pivot-mounted plastic blades.
For the test Stihl supplied a backpack-type AR1000 battery. This is lithium-ion, incorporates a 6-led battery charge indicator and comes with a handle and waterproof cover. It’s comfortable and with the harness correctly adjusted you forget you have it on,” Jamie said. “It’s easy to take on and off and even though we had a week of exceptionally hot weather during the test period, wearing it was never a problem.”
Jamie said that because battery-powered brushcutters consume no power unless they are cutting, all the battery capacity is available for work. “This extends on-site time between recharging where petrol models are usually left idling for brief periods between use and continue to consume fuel,” he explained. “It also helps that with no clutch, the battery model can operate at lower engine revs for lighter work and there are three power settings allowing the user to reduce the operating power and speed for lighter tasks – maximising available working time, and reducing working noise.”
Adequate capacity
The battery supplied was the smallest of Stihl’s three backpack versions but still achieved approximately 90 minutes of cutting time at full power, equivalent to several hours’ typical use. Jamie said that charging overnight and again at lunchtime meant there was plenty of capacity for a typical day’s trimming although for continuous heavy work a larger battery or a spare would have been helpful.
The FS111 achieved approximately one hour’s work at full speed between refuelling, which Jamie deemed excellent in terms of fuel economy. “It’s got a very large fuel filler,” he said. “It’s much easier to access than any of our current brushcutters making it easy to refuel at the work site and it’ a great design feature. One of the best I have seen.”
For convenience; simply pressing the safety switch and pulling the trigger of the battery model was unbeatable, but that didn’t stop Jamie complimenting the ease of use of the petrol version. “Even after running out of fuel, whether hot or cold it started easily after a press of the fuel pump and was never any trouble.”
Use and maintenance
In work, the petrol model proved comfortable, quiet compared to the estate’s current machines and easy to use but Jamie said the electric version was quieter and more comfortable being almost totally free of vibration. He pointed out that whereas the petrol model continues to idle between cutting periods so there is always some noise, the battery version became silent when not cutting which made it less tiring.
“Both were well balanced and even with the lighter electric motor at the top, the position and angle of the cutting head was easy to control. One thing I noticed was that after a long period of use I was less physically tired as less effort was required swinging it from side to side. “
Apart from recharging the battery model requires little maintenance but the petrol machine was simple to prepare for a day’s work. “Everything is well designed and accessible,” he said, “and a feature I particularly liked was the transparent fuel tank making it easy to check the fuel level at a glance.
“The AutoCut head is easy to reload with line but there is plenty of capacity and even though it is lighter than the line we usually buy, it wasn’t refilled during a week’s heavy use.”
The electric model’s PolyCut head was liked by all the operators who found it effective and easy to use. Refilling was especially easy. “It’s very good on green vegetation,” said Jamie, “but we found quite quickly that it didn’t like tree stumps or walls so had to be careful where there were obstructions. We tried the cord head too, but found this was the one situation where the power wasn’t quite as good as the petrol machine and it struggled when presented with dense vegetation.”
Verdict
Jamie said that by the end of the test he favoured the FSA130 battery model over the petrol, tending to use this from the start of each working period until the battery was flat, and then switch to the petrol. “I got on well with both and would be happy working with either, but the battery version was quieter, more convenient and more comfortable due to the lower vibration and I was very impressed. The petrol performed well too, and had a very slight power advantage for the heaviest work, so having it as a reserve worked well.”
Asked whether he would request a battery model when the estate’s brushcutters are next updated Jamie confirmed that he would, but with a higher capacity battery. “The battery life was impressive,” he said, “but during the final 20 minutes of working it was obvious without looking at the battery indicators that a recharge was needed.”
Ahead of Agritechnica later this year Fendt displayed its latest innovations to press from across Europe at the company’s German headquarters. David Williams attended.
Considerable investment in research and development should ensure Fendt’s products and services remain at the cutting edge of agricultural technology. This year an estimated €73.7m will be spent on R&D, up from €72.2m last year.
Sales are impressive for the premium brand in a competitive market, and last year 16,806 tractors were produced of which 66 per cent were exported from Germany, whereas the 2019 estimate is ‘significantly more’ than 18,000 units with 68 per cent exported.
Combines are in growing demand too, and with 353 sold in 2017 rising to 427 in 2018, this year’s total is likely to be up to 460, helped by the award winning Ideal model available commercially for the first time this season.
Tractor news
A grand reveal of the latest 900-series tractors was widely predicted ahead of the event and an impressive display of the first 35 leaving the factory on lorries for destinations all over the world didn’t disappoint.
The new 900-series 5-model line-up includes a flagship 942 Vario pushing maximum power in the series up from 396 to 415hp. Power throughout the series is from MAN engines, designed especially for the application. These 6-cyl, 9.0-litre (up from 7.8-litre) power units have variable geometry turbocharging and require an oil change only every 1,000 hours.
Fendt’s iD low engine speed concept is used in the new 900-series with rated performance at just 1,700rpm. Idling is at 650rpm and maximum 60kph transport speed is achieved at just 1,450rpm. Maximum 1,970Nm torque is at 1,100rpm on the 942 Vario.
Completely new to the 900-series is VarioDrive transmission, borrowed from the larger 1000 Vario-series. This distributes drive effort separately to the front and rear axles, depending on operating conditions. Because the front and rear axles are decoupled there is no power wasted due to axle ‘wind-up’ and at higher travel speeds drive to the front axles fully disengages unless it is needed for traction or during braking. An advantage of the design is ‘pull-in turn’ which applies extra power to the front axle during sharp turns to pull the tractor in the steering direction for extra manoeuvrability. A new heavier-duty front axle is fitted to suit the additional power. Fendt will submit the new tractors for independent performance testing in the coming months and predicts significant fuel savings mainly due to the new transmission.
The cab is new with technology capable of displaying machine performance data in realtime through the base telemetry package.
Fendt Connect allows data sharing to analyse and manage machine use making it easier to manage machinery fleets. It also provides access to dealer services.
Smart Connect is also available for the new 900-series tractors allowing the user to link an iPad to the tractor using an internal wifi network. Machine parameters including position, worked area, speed, fuel consumption and engine load are sent straight to the iPad during use and the screen serves as an additional display area for the Varioterminal. Smart Connect is standard on all ProfiPlus variants.
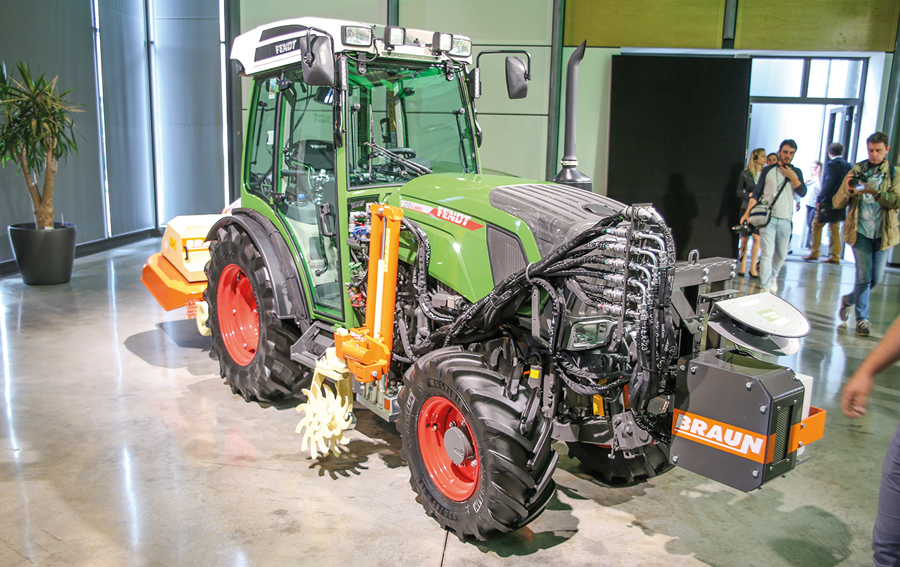
The Fendt 200 Vario with automatic control of complex implement combinations was developed in conjunction with Braun.
Added compatibility
Despite its size the new 900-series models can be set up for a wheel-track down to just 60in.
VarioGrip tyre pressure regulation is an option allowing pressure adjustment while driving. The latest version is capable of inflating dual row-crop wheels from the cab.
Fendt Grip Assistant is also available for the new 900-series through the terminal, allowing the user to determine the ideal ballast and tyre pressures at pre-defined operating speeds. It also allows the user to determine optimum working speed and tyre pressures where ballast is already fitted.
For maximum grip a new 750/70R44 2.2m diameter tyre has been developed for the range.
Load-sensing pumps provide 165- or 220-litres hydraulic oil flow capacity. Optional 430-litres/min flow can be specified. Two autonomous axial piston pumps provide the flow; one with 220-litres/min and the other 210-litres/min, mounted either side of the rear transmission housing allowing convenient hose attachment from each side. Fendt explained that the slight difference in pump output is to prevent resonance when the pumps work together for maximum flow. Having two pumps provides greater flexibility in terms of supplying different rates and pressures and with such high flow available, the system complements Fendt’s iD low-speed concept.
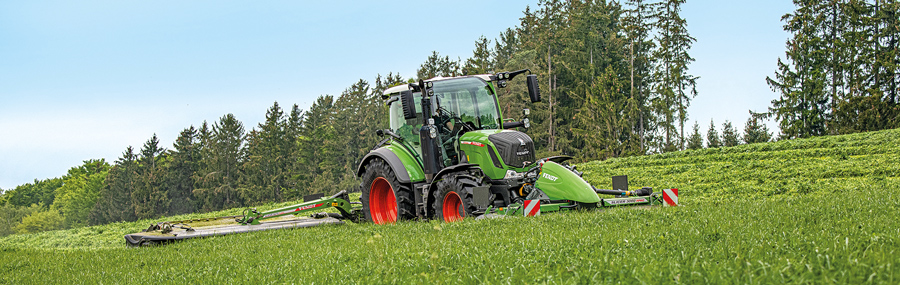
The new 314 Vario with 10hp boost available when needed.
Comfort and convenience
Along with the additional connectivity and driver aids, the new 900 Vario series tractors are available with an infotainment system operated from the terminal. As well as improving clarity of telephone calls, additional upgrades include a high-end speaker system.
A new storage area below the cab on the right-hand side provides space for a tool box or 12-litre washing station.
Also new is an in-cab air supply for convenient hose attachment and making it easier to blow clean the cab floor. External mirrors are electrically adjustable including a telescopic arm mount allowing extension from the seat to see around wide trailers or implements, and quick retraction to avoid damage once the trailer is removed.
Improved anti-theft protection includes a safety locking system and combined immobiliser. This uses a coded key, unique to each tractor, for the cab, ignition, bonnet and fuel tank.
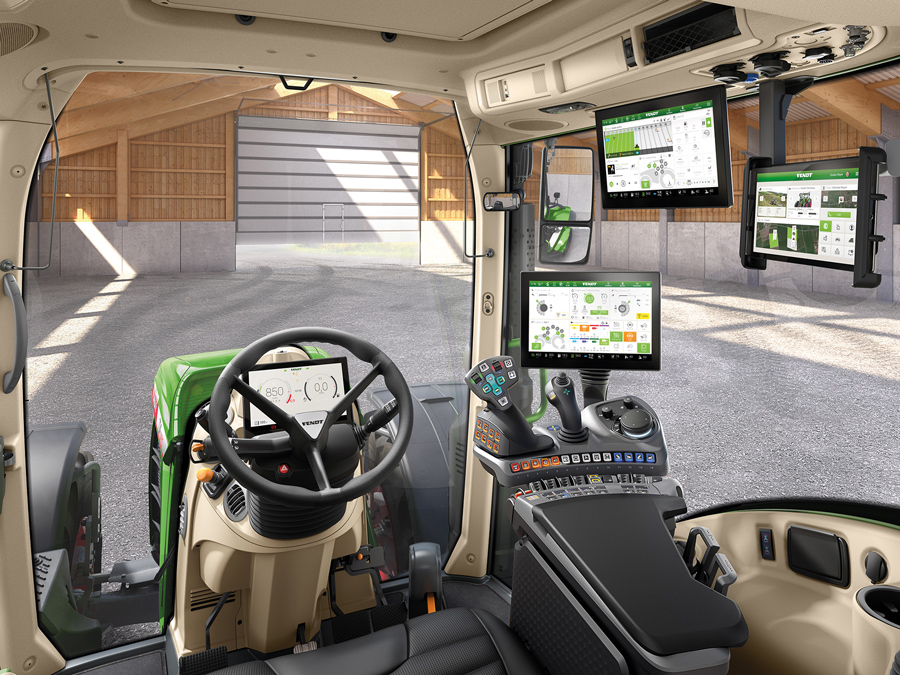
Fendt 700 Vario ProfiPlus models will be the first available with FendtOne making it easier to control multiple implements while making the most of guidance and data sharing through multiple digital displays and the new 3L multi-function joystick.
Task management
Implement control and monitoring can be through the standard Isobus connection. Tractor Implement Management (TIM) is an upgrade option, allowing tractor functions including operating speed to be controlled by the implement.
Fendt TI Headland smart headland management is also available through which Variotronic activation of a programmed headland sequence can be linked to VarioGuide position monitoring. This allows implements to be automatically raised and lowered, for example, when the appropriate headland position is reached.
Deliveries of the new 900 Vario series have already started and most UK dealers have ordered at least one demonstration machine.
The new engine is a significant update, but the integration of the VarioDrive transmission offering improved performance combined with potential fuel and tyre wear savings will also be a major attraction to potential users. In fact, Fendt suggested that its unique drive concept is likely to filter down through to its smaller tractors in time, allowing smaller farms to benefit from the advantages too.
Other tractor news
Other large tractor news includes the flagship 1000 Vario series of which more than 2,000 have been delivered to date. Several new options include those introduced for the new 900 Vario, including; electrically adjustable mirrors with telescopic arm mounts, a security coded key and immobiliser and the infotainment and speaker packages.
The Fendt 900 Vario MT rubber-tracked crawler is now available with the joystick companion to the 10.4in terminal allowing headland sequences to be more easily programmed.
There are also two new hydraulic valve control options.
FendtOne
Looking further to the future a new FendtOne control concept was shown for the first time. Available in late 2020 for the most popular 700 Vario, and 300 Vario series, FendtOne is a new, intuitive operating system which allows users to plan work and field data in the farm office then transfer it direct to the tractor by mobile network with both ends of the process sharing similar layout and appearance for ease of use.
For ProfiPlus models it offers Smart Farming applications such as tracking capability, the Fendt Task Manager for efficient task management and Guide Sync for field data management. The FendtOne platform can be tailored to suit individual situations helping users get the best from their machines. The Agrirouter data exchange platform is a key part of the system making it ideal for contractors to share data with customers using a variety of different farm management programmes and software.
The most noticeable difference between current models and those equipped with the FendtOne system is additional display space and increased display options. Up to three displays can be added within the standard configuration all linked to a central computer. These include a new 9in digital dashboard display which provides essential road travel and Fendt Guide features with operation through an armrest-mounted push-dial. Two 12in displays; one on the right armrest as well as an optional terminal in the roof offer up to 6 freely configurable display fields. Both 12in screens can be controlled through the new, optional 3L multi-function joystick which also incorporates additional functions, or by direct touch to the screens. The new joystick is to the right of the standard crossgate control joystick and has 3 operating levels and up to 27 functions.
Functions are divided into groups by colour making it easy for operators to tell if buttons have been re-assigned and to avoid errors.
Fendt says the improved display options and additional screen area will help operators get the most benefit from the ever increasing number of terminal applications available, and make it easier to handle data and control more complex attachments by providing a better overview of tasks without constantly switching screen views or having to divide screens into smaller sections.
Isobus connectivity is improved including a front connector making it easier to control and monitor front-mounted implements direct from the tractor armrest.
Like the larger tractor series, the new 700 Vario will be available with an optional infotainment and high performance speaker package.
New 300 Vario flagship
Smaller tractors haven’t been forgotten in the upgrades for 2020 and the addition of a new flagship 314 Vario to the 300 Vario series provides an additional 10hp available on-demand through Fendt’s DynamicPerformnce power-boost. DynamicPerformance isn’t restricted only to particular operating situations, so up to 152hp is available whenever it is needed to meet demand for PTO, hydraulics, engine cooling, and air conditioning. It constantly monitors the power requirement, delivering extra if needed. This makes it available for stationary PTO work for example, such as powering large mixer wagons as well as for transport and field work.
FendtOne for the 314 Vario introduces Agrirouter to the series for communication and data exchange and a new multi-function joystick is available offering similar advantages to the new 700 Vario’s system.
The three-terminal option including a 9in, and two 12in displays is similar to the top-end system from the 700 Vario.
A high-end infotainment and speaker system can also be specified.
The new 314 Vario will be available in Profi and ProfiPlus variants in late 2020.
Automated operation
Combined automatic control of Fendt 200 Vario tractors and complex vineyard implements is being introduced by Fendt which has worked with Braun on the development.
The initial system is designed for viticulture where increased mechanical weed control is replacing herbicides. The tractor and implement combination is fully controlled by the system from accurate steering between vine rows to precise positioning and movement of front, rear and mid-mounted implements with operating speed also regulated automatically to suit the task and working environment.
Information from which operational adjustments are decided is provided by a laser, a gyroscope, the Vineyard Pilot Assistant control unit and a terminal.
The laser constantly scans the environment detecting soil contours, vines and stakes and active intervention is only needed from the driver at the headland. Operating speed is almost twice that possible when similar combinations are controlled manually and with more activities combined in one pass, compaction through additional journeys is reduced.
Ideal 10
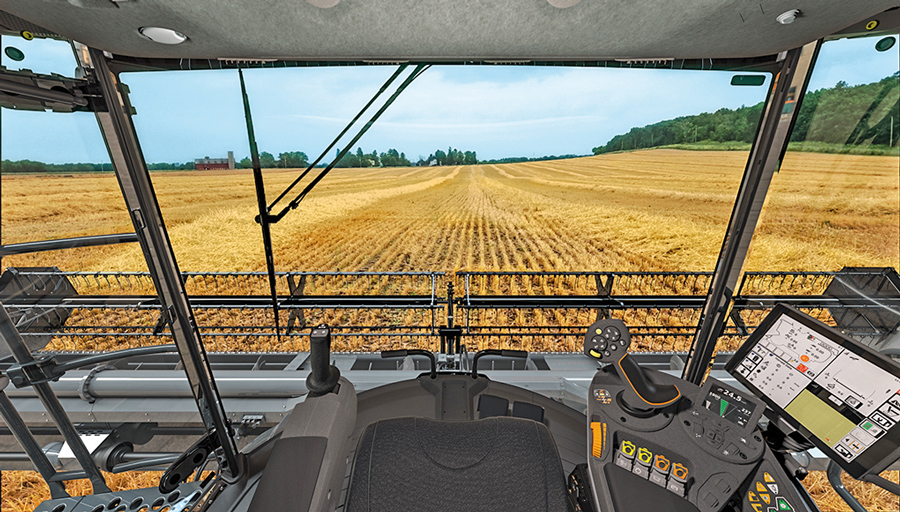
For 2021 the Ideal 10 will be available with headers up to 12.2m, and no steering wheel.
Fendt’s Ideal combines are working commercially for the first time in the UK this year after a limited number of machines were demonstrated by selected dealers in 2018. So far Ideal 7-, 8- and 9-series models have been shown but an Ideal 10 with a new MAN 16.2-litre power unit producing up to 790hp will be available to order from July 2020 for delivery in time for the 2021 harvest.
The Ideal 10 has a new cleaning system working with the innovative Dual Helix separator. An unusual design feature of the Ideal 10 is that it has no steering wheel, improving forward visibility to the road and the header. Replacing the steering wheel is a steering joystick on the left-hand armrest, and for access to the seat the armrest and joystick fold up out of the way. Fendt IdealDrive joystick steering is said to comply with all traffic regulations and is only available for Ideal combines.
Katana 650
News regarding Katana forage harvesters included an upgrade to the 650 improving performnce and reliability.
Engine power is up by 25hp to 650hp from its MTU 6-cyl power unit. A variable drive cooling fan with reversing function is now standard controlling air flow by adjusting the blade angle.
For harvesters working with wider maize headers, improved performance on undulating ground is provided by a new intake with up to +/- 7 degrees of rotation available.
The crop pick-up is optimised and the processing area is enlarged with two 300mm rollers, one of which has an additional V helical groove to increase lateral destruction of the crop.
The spout has a larger cross section aiding crop flow and Fendt national sales manager Martin Hamer explained that this improves performance in wet grass and will increase appeal for UK users.
From in-feed to the chute flap the redesigned crop flow to suit the new roller conditioner increases throughput by up to 21 per cent, equivalent to 12 per cent reduced fuel use compared with current model performance. Chop length up to 30mm can be obtained.
“For crops such as direct cut rye the new roller cracker can be set up for exceptional cracking quality, and will increase appeal to UK farmers and contractors,” pointed out Martin.
Improved blade sharpening performance and an extended blade and sharpening stone life result from a new sharpening system. The stone constantly readjusts during use and is more aggressive on the outer blade sections to maintain an even profile. Optimal blade sharpening improves chopping quality and extends the service life of the stone and knives by up to 25 per cent claims the company.
For improved performance on steep slopes Fendt has added BalancedGrip to the Katana 650 which adjusts the proportion of drive allocated to each axle and prevents the wheels spinning when axle loads are reduced, protecting the sward from damage.
The new Katana 650 is available to order from November 2019.
Sprayer news
A more powerful Rogator 600 self-propelled sprayer is being added to the line-up. The Rogator 665 has a 307hp, 7.4-litre 6-cyl engine and, from 2020, all Rogator 600 models will be powered by similar power units with a range of different power outputs.
Fendt OptiNozzle will be available from January 2020 offering Rogator users optimal application results with minimum chemical drift. The most suitable nozzle or nozzle combination is automatically selected once the operator has specified the output, degree of drift reduction needed and a working pressure range for optimal droplet size. Then the system constantly adjusts in work responding to changes in speed or output levels.
For Rogator 300 trailed sprayers, Tractor Implement Management (TIM) is being added allowing compatible Fendt Vario tractors to be controlled by the sprayers. The sprayer automatically selects optimal speed and adjusts the nozzle parameters accordingly, including the preferred drift reduction and output. Depending on the nozzles used the sprayer adjusts the travel speed to the calculated target speed ensuring the product being applied always benefits from a suitable level of drift reduction. Active TIM control allows the operator to adjust the speed; choosing from pre-set ranges and the selected speed is maintained while the sprayer adapts the nozzle or combination of nozzles to suit.
Also new for Rogator 300 trailed sprayers is a wider 36m boom with triple folding.
Grass harvest updates
A new front mower is being added to the Fendt Slicer range. The Slicer FQ is designed for medium to large dairy farms and contractors in 3.1 and 3.6m working widths and with tine or roller conditioners. Lateral shift of +/-20cm left and right is standard and allows correction on side-slopes for drift.
Three-dimensional ground adjustment maintains accurate ground following laterally and longitudinally. As the cutter bed moves up and down following ground contours, the mower tilt automatically adjusts between -6 and +15 degrees with the mower’s vertical travel. This is claimed to result in constant cutting height even in difficult conditions. Compensation for undulating ground includes up to +/-13 degrees cross-swing and 750mm vertical travel.
The mower can attach direct to the tractor’s front linkage, keeping the centre of gravity close to the tractor.
Fendt’s TurboLift hydropneumatic ground pressure adjustment is standard with tool-free adjustment and minimises sward damage even in very wet conditions.
The addition of Lotus tedders to the Fendt grass harvesting line-up for next year was welcomed by the Fendt UK sales team. “The Lotus name is highly respected and there is nothing to touch it for tedding performnce in typical challenging UK conditions,” explained Martin, who said having it available for next year’s grass harvest season will be appreciated by customers and dealers.
Three Lotus models in the Fendt range cater for most UK demand. These include the fully mounted Lotus 7.7m 770, and trailed 10.2m 1020T and 12.5m 1250T models. All have Fendt performance tines; 6 on each rotor on mounted models and 7 on trailed. The tines have a unique profile guaranteeing thorough pick-up of the mowed crop and ability to effectively turn heavy, wet forage. Fendt’s tine design is claimed to result in up to 15 per cent higher work rate than standard tines.
Baler updates include Intelligent Hay, allowing data specific to each bale to be recorded and stored easily. During baling, data about each square bale is recorded including GPS position, moisture, bale flakes as well as information regarding bale length, weight and additives used. Using special twine in the third or fourth twine position, an RFID chip is woven into each bale providing an identification code. When this code is cross-referenced against data stored in a cloud-based memory the bale data is available to view.
Other baler news includes the ProCut cutter unit being added as an option for the Fendt Squadra high-performnce square baler. The 26 knives are arranged in the drawer in 2 groups, each of which can be controlled separately to provide a fine cut or for double the cutting length when only half are selected.
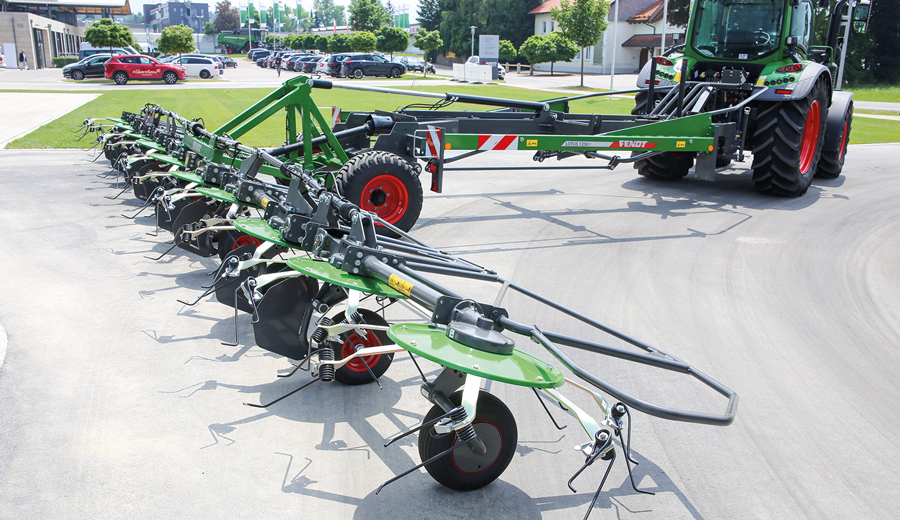
Lotus tedders are a welcome addition to Fendt’s green harvest range.
Fendt designed and branded rubber-track crawlers were announced last year, some with new technology borrowed from the German manufacturer’s largest wheeled tractors. David Williams has been finding out how they perform.
Fendt designed and branded rubber-track crawlers were announced last year, some with new technology borrowed from the German manufacturer’s largest wheeled tractors. David Williams has been finding out how they perform.
The Fendt crawler line-up includes 7 models in 2 sizes, from 380–646hp. Both result from Challenger’s incorporation within the Fendt brand but, whereas the new 1100MT models are mechanically similar to the previous MT800-series, the smaller MT700-series has been replaced by all-new 900 Vario MT models.
Externally the most noticeable change, apart from green paintwork, is a Fendt cab but under the body panels is a Fendt Vario CVT transmission, track and cab suspension and Fendt controls.
With fewer changes the 1100MT models have been available since early this year but the 900 Vario MT models have only recently arrived on farms.
Farmers Guide visited a north Suffolk farm which was one of the first to take delivery of one of the new models.
Mark Hadingham and his son Ben farm in north-east Suffolk and just over the Norfolk border, trading as Retreat Farms and Flixton Farms Ltd. Approximately 1,600ha is farmed across 4 sites and the land is a mix of owned and contract-farmed. Most soil is Beccles-series clay but there is also some lighter land at Blyford nearer the coast.
“Our soil is a delicate asset,” commented Mark. “We have to look after it carefully so we moved to tracks approximately 20 years ago. We have a policy of not carrying out cultivations with wheeled machines and our wheeled tractors are used mainly for tasks including transport and hedge cutting. Since moving to tracks our soil structure has benefitted and although tyre technology has improved considerably in recent years, we don’t feel they provide the same soil protection. And it’s not only the soil that gains an advantage; tracks allow us to work more efficiently and get more from our machines.”
The first rubber-tracked crawler purchased was a Caterpillar, later replaced by a Claas-branded version. Then another brand was operated briefly before settling on Challengers, supplied through East Anglian main dealer Thurlow Nunn Standen.
In recent years the fleet has included two 765s and a larger 865. A 765D was recently part-exchanged for a new Fendt crawler which arrived in early August, and which complements the farm’s 765C and a larger 865C.
Cropping includes winter oilseed rape, sugar beet, vining peas, winter barley, spring barley and some rye and crops are established using Vaderstad 6 and 8m Rapid drills.
Cultivations are mainly min-till although ploughing is carried out where needed. The plough is a Gregoire Besson 9f reversible and cultivators include a 6m Vaderstad Top Down, a 6m Vaderstad Rexius Press, an 8m Vaderstad NZ seedbed cultivator and a 6m RapidLift toolbar mounted to the farm’s 6m Vaderstad Rapid drill. Mole ploughing and subsoiling are carried out where needed.
“During the autumn we often have all three crawlers working, but only bought the 800-series crawler because the smaller 700-series wasn’t available with the same power,” explained Mark. “We didn’t want to go to the bigger model to do more work, but needed pulling capacity for the plough and drilling with the RapidLift toolbar fitted.”
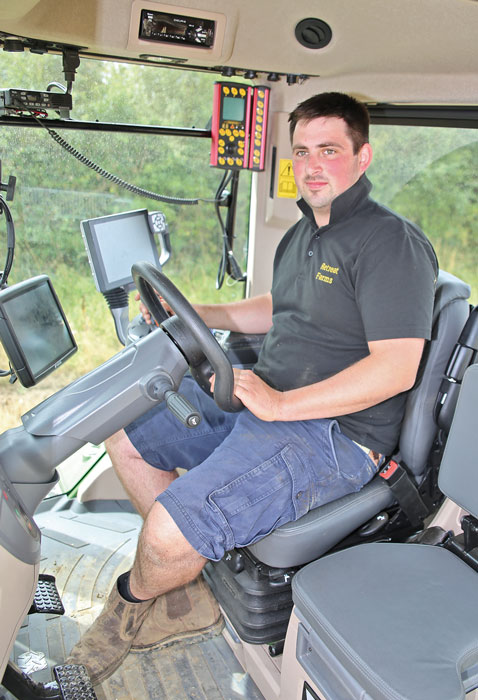
Main user Jordan Burcham said the new models offer 100 per cent improvement for operators and that it will be hard to spend a day on the farm’s Challengers after a week on the Fendt.
Easy decision
When Mark heard of the new Fendt models he was optimistic that pulling capacity would be increased and attended a demonstration in Lincolnshire earlier this year. “It was good to see the Challenger replaced, but improved and brought up to the next level,” he said. “We have considered other brands and keep an eye on alternatives but believe the new Fendt models offer the best design and performance.”
The farm ordered a new 943 Vario MT, the flagship of the 900-series with 431hp. Mark believes the new tractor’s additional power will allow it to share larger implements with the 800-series, making field operations more efficient.
By the time of Farmers Guide’s visit the new tractor had worked 110 hours, and field work had included mole draining and cultivating with the 6m TopDown.
“It’s improved 100 per cent over the previous 765D,” commented main operator Jordan Burcham. “It’s hard to compare as it is so different but I know that using the older models again will come hard. The transmission is obviously very different as the CVT and engine adjust continuously for optimum performance. Previously I was always changing powershift gears and a low ratio had to be selected for pulling away otherwise it could stall. Then moving up through the gears took a while until the operating speed was reached.”
The new Fendt Vario crawlers have a similar transmission to 1000-series wheeled tractors. Twin hydraulic motors control the power split between hydraulic and mechanical giving variable speed control with a bias to mechanical transmission for high torque at low speeds and hydraulic at higher speeds, saving fuel. The operator can select manual mode; adjusting the engine and transmission independently or select ‘TMS’ by pressing a button on the control panel, allowing engine and transmission management by the tractor’s systems for lowest engine revs and maximum fuel economy.
Response to varying loads is adjustable. A constant engine speed can be maintained regardless of load, or allowed to reduce within pre-set limits, saving fuel.
Travel speed control is by the Vario multi-function joystick, but the operator can also select control through the foot drive pedal. “The foot pedal has advantages on the road,” explained Jordan. “On narrow lanes I can slow down while passing cars, then just depress the foot pedal again to pull away. Everything adjusts automatically leaving me free to watch the road whereas the previous Challenger with powershift needed me to concentrate on shifting from the lowest gears all the way up the range, and avoid stalling.”
Speed control sensitivity is adjustable in four stages, using a small selector on the joystick. For rapid reaction to joystick commands the selector is set to most aggressive and for more relaxed operation and a smoother ride, response is reduced.
Superb ride quality
The new Fendt tractors have an all-new track and carriage design, including suspension. ConstantGrip comprises a double pendulum within each track assembly allowing the tracks to mould around undulations, maintaining even ground pressure along their length and across the track width.
Large coil springs and shock absorbers support the chassis and provide up to 23cm vertical movement for each track, with up to 11 degrees swing angle also available, while a torque rod stabiliser ensures lateral stability.
The cab is suspended as is the seat and Fendt claims comfort and noise levels equivalent to a premium wheeled tractor.
“Ride quality is great on the road and in the field,” confirmed Jordan. “When the tractor first arrived the ground was rock hard after the long summer drought but track vibration was hardly noticeable. The improved ride means I can make the most of the power to achieve higher working speeds than before, so the tractor is more productive.”
The cab is almost identical to that of the 1000 Vario tractors including a 10.4in Varioterminal touch-screen to set up and monitor operating parameters. “It’s clear and easy to see, even in bright sunlight,” commented Jordan, “and the menus are logical so it doesn’t take long to work out how to alter the settings.”
The farm has its own RTK network and the tractors use Topcon GPS field mapping. Variotronic Turn Assistant on the new Fendt can be used to negotiate headland turns automatically, and was proving popular with Jordan.
Visibility all around was described as excellent, including to the implement at the rear and Jordan said he especially likes the mirrors, which provide excellent side and rear views on the road and of the implement in the field. Some late evening work has been carried out and the working lights are impressive.
Fuel and time savings
Mark said that although it is hard to accurately compare fuel consumption between tractors, he believes the Fendt crawler uses significantly less than the Challengers, and explained this is partly due to the low revving engine and TMS mode which makes the most of the engine’s performance. Pulling the 6m TopDown at 6–7in depth on heavy soils at 10kph, the engine was running at just 1,300, whereas Mark commented that the Challenger 765D probably couldn’t have pulled it at similar speeds, but typically required 2,100rpm in less demanding situations.
Adblue use also appears lower, added Mark, but he said both tractors require a top-up each time the diesel tank is filled. Daily checks are improved and Jordan explained that hydraulic and transmission oil levels are checked in seconds using sight gauges at the rear, and the engine oil dipstick is easy to get at without removing any covers. The cooling system is similar to the Fendt 1000-series wheeled tractors with a concentric hydraulic-driven fan pushing cool air through from the front. So far this has remained clean, even in dry, dusty working conditions.
Part of the track system’s redesign includes plastic wear discs at the rear of the centre rollers. Thurlow Nunn Standen’s Challenger and Fendt specialist Dave Lovell explained that side thrust during work forces the rubber drive lugs against the backs of the rollers and on the Challenger they could overheat, damaging the outer rubber band and causing premature failure. The new plastic wear discs help prevent heat build-up and should significantly extend working life.
Extra flexibility
The 6m TopDown on the heavy soils was a good match for the new crawler and during Farmers Guide’s visit, the cultivation depth was set to maximum to see how it affected performance. At 10in on the headlands the Fendt coped easily at 8–10kph, and its capability impressed Mark. “It didn’t struggle and the tractor continues to surprise me. We tend to be restricted during drilling using the more powerful 800-series Challenger, as we have to start in a low gear and change up again through the powershift steps after every headland turn.
“We could drill faster, but above 12kph there is a big step to the next gear as the clutch packs swap over which affects drilling performance, so that has become our maximum. However, I think the new Fendt Vario model with its CVT transmission will provide much greater flexibility and from what I have seen so far it has the power and traction to handle the drill. I think we will achieve higher work rates than were possible previously, while saving fuel and without increasing tractor size and weight.”
Investment stacks up
The Fendt was purchased with an 8-year, 8,000-hour warranty. “Previously we updated Challengers every 3 years or 3,000 hours, but with its longer warranty giving additional peace of mind we will probably keep the Fendt longer, which should help reduce ownership costs,” explained Mark.
“I’m convinced the CVT transmission will provide significant advantages for Fendt owners,” said Dave Lovell. “It’s so simple and allows users to get the most from the power available while minimising fuel use.
“Ride quality is excellent and no other tracked machine comes close for comfort. Ownership and running costs should be low and the long warranty provides reassurance. We believe the new models will be popular.”
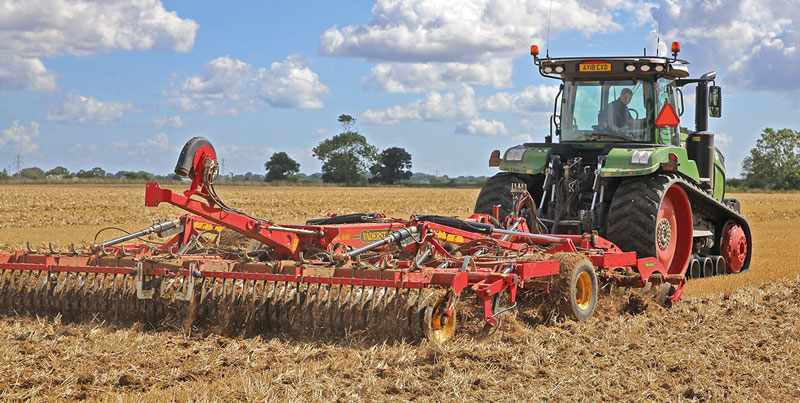
With the Vaderstad 6m TopDown in at full 10in working depth, the Fendt didn’t struggle.
John Deere’s latest wide-body 9000-series forage harvesters offer a beefed up design over their 8000-series predecessors, with additional features, more power and bags more torque for higher outputs. David Williams tried them out.
Four new models, the 9600, 9700, 9800 and 9900, replace 8600, 8700 and 8800 versions. Externally new styling is the most noticeable indicator but the purr of low-revving V-12 power units replacing previous straight-6 engines on three models is also significant.
The new models are 625–970hp, gaining 127hp over the previous most powerful 8800, and John Deere claims up to 10 per cent extra productivity over models replaced, combined with 10 per cent fuel savings.
On the three largest models, Liebherr 24.2-litre V12 power units produce maximum power at under 1,400rpm and a John Deere PSS 13.5-litre 6-cyl engine is used in the 9600.
To make the most of the low-revving engines a new transmission was developed allowing all major components to operate at optimum speeds.
Engines are mounted longitudinally for optimum cooling efficiency and all can meet latest Stage 5 emissions regulations. “We couldn’t meet Tier 5 using the Cummins engines fitted to 8,000-series models and the Liebherr V12 has bags of power, a very flat power curve and maximum torque at just 1,350rpm,” explained John Deere harvester specialist Ross Skimming. “Previously maximum torque was between 1,700 and 1,800rpm and if the revs dropped below 1,700 then there wasn’t as much torque in reserve.”
To cope with the extra power the processing system has been strengthened. Crop is fed through an 850mm channel and a stronger shearbar, sharpening system and drum is incorporated.
ProDrive fully automatic transmission achieves 13mph in field mode at 1,200rpm and 40kph for transport at 1,400rpm, providing fuel savings.
Demanding field test
Farmers Guide tried the new 870hp 9800 in a dense crop of rye grown for a Worcestershire AD plant. The huge torque reserves made it easy to operate in variable crop and noise levels were low in and out of the cab. “Because the new engines are so low-revving, there is no need to reduce engine speed at each headland turn and full power is always available,” Ross explained.
Updates to the Active Fill Control trailer filling system include the ability to automatically fill trailers at the rear now, as well as at the side. New twin cameras supply loading information to direct the spout and the update will allow harvester operators to keep their eyes on the header rather than having to watch the trailer during opening up. The demonstration field posed quite a challenge for the system as extremely dry conditions and strong gusting side winds caused the crop to be blown sideways necessitating constant spout adjustment, but it compensated well and the dust didn’t seem to confuse the cameras.
Harvest management
The cab is similar to before but the demonstration machine was fitted with the latest HarvestLab 3000 NIR (near infrared) sensor. This provides real-time measurement and recording of crop yield, moisture and constituents including protein, starch and fibre either as totals or on field maps.
The latest HarvestLab system also enables AutoLOC (automatic length of cut) settings to be monitored, and adjusts silage additive dosing on the move, based on dry matter content.
A brand new display was fitted to the demonstrator. The 4640 10in screen is similar to the 4600 version supplied in latest 8000-series tractors but the 4640 also operates as a standalone unit, enabling swapping between machines. It’s larger than the current flagship 2630 version, with additional features for greater flexibility including the ability to continuously trickle-feed information rather than waiting for a summary of areas completed. A brand new app; MyOperations, allows constant remote monitoring of machine settings and task progress, from anywhere with a data connection.
The 2630 is the minimum specification to run HarvestLab and Ross suggested that although the demonstration machine had the new screen and current 2630 fitted, users are more likely to have a standard smaller screen for machine operation with the 4640 for HarvestLab.
Superior chop quality
“Consistency of chop is excellent,” suggested Ross. “Chopping the rye to 6mm for the AD plant, every sample we checked was almost spot on. The previous 8000-series harvesters were already praised by users for their chop performance but the new models are even better.”
For those harvesting maize John Deere has added to its range of kernel processors. The new XStream KP was developed in cooperation with US-based Scherer and has a large 250mm diameter and 50 per cent roll speed differential increasing processing intensity by 10 per cent at all chop lengths.
Also available are the standard Premium KP unit with a sawtooth teeth design and the XStream KP which can have the sawtooth profile or a new XCut design with a spiral groove across the roll surface. The XStream KP also has built-in temperature monitoring, keeping the operator informed of temperatures in work to help prevent overloading and downtime through bearing failure.
Potential higher maize yields through optimum plant spacing attracted East Anglian farmers and contractors to a drill demonstration organised by Ernest Doe and Lemken. David Williams was there.
Lemken’s Azurit maize drill was first shown to the press in autumn 2015 and is designed to optimise maize population and yields by planting seeds in double rows to provide maximum growing space for each plant. Extensive trials in mainland Europe during development and since its launch have proved successful. This year four Azurit drills are working in the UK to establish the crop, two of which are demonstration machines and attracting considerable interest from potential users.
DeltaRow seeding
The DeltaRow seeding system includes a pair of residue wheels ahead of the coulter to clear trash followed by a fertiliser coulter, which applies nutrients between the twin seed rows. A trailing trapeze packer closes the fertiliser groove and rings consolidate the furrows.
Seeds are supplied to the singling units ‘on-demand’ and two synchronised perforated discs with adjustable mechanical or optional automatic scrapers distribute seed alternately to the two double-disc coulters of the seeding unit resulting in a repeated triangular seeding pattern.
Spacing between the seed rows is 12.5cm and space between each double row is adjustable between 37.5–87.5cm. Establishment by the DeltaRow system provides approximately 70 per cent increased growing area compared with conventional single-row planting, explains Lemken UK general manager Paul Creasy. To ensure seeds are spaced accurately the singulation units sit above the coulters providing a short 60cm direct drop down the seed tubes.
Ten-step hydraulic coulter pressure adjustment provides up to 135kg per unit and seeding depth is regulated by a large solid depth wheel between the coulter pairs. A V-shaped roller closes the seed rows and provides consolidation.
An advantage of the dual seeding units is that each singling disc only handles half the number of seeds of a conventional planter, allowing smaller discs revolving at lower circumferential speeds to be used, improving accuracy.
At Lemken’s press launch Azurit product specialist Lena Busch said almost perfect accuracy has been achieved in trials at up to 18kph, although more typical drilling speeds have averaged 12–15kph. “From the start of development our objective was to achieve 100 per cent accuracy,” she explained.
Because the double seed rows are wider than conventional single rows, where each tramline occurs the row closest to the wheeling is switched off, when an optional electric seed scraper is specified. However, rather than lose potential yield through reduced plant numbers the opposite disc rotates at twice the normal speed to maintain the population per hectare. An obvious concern of potential contractors regarding the wider plant rows is compatibility with harvester headers but during trials all header types have proved suitable.
“The Azurit drill is designed especially for maize and our trading area includes many large-scale growers including farmers and contractors,” explained Ernest Doe Wymondham branch sales manager Ross Johnson. “The weather on the demonstration day was ideal for maize drilling, but with more unsettled weather and rain expected, growers were under pressure to make the most of their own drilling opportunities.
Lemken’s DeltaRow concept and its potential for extra yield is very attractive and while those who came were keen to inspect the rows and check the seed spacing and positioning for themselves, many who couldn’t make it are planning to travel to the field to check the emergence in a few weeks’ time. Visitors were from as far afield as south Essex, Cambridgeshire, Norfolk as well as Suffolk, and we have a lot of enquiries to follow up in the coming weeks. This drill gives us a full package to offer professional growers from planting, to harvesting by our New Holland Forage Cruisers all backed up by unbeatable after-sales service.”
Claas demonstrated new and updated models in its harvesting ranges at a press event in early August. David Williams reports.
Claas continues to invest heavily in research and development and has announced new combines, mowers and balers promising benefits for farms of all sizes. A new control concept has been added for the mid-sized Tucano models, with even more automation to help operators of Lexion machines.
The Tucano range is extended with a new top 580 model. Claas combine product manager Adam Hayward explained that this fills the gap between the previous most powerful Tucano 570 and the larger Lexion range.
Tucano models are available with 5 or 6 straw walkers or as hybrids, with a drum separator then a rotor, and in narrow or wide body widths. For 2019 the Tucano line-up includes 13 variants, with 5 available as new Montana hill-side versions.
Engines are all from Mercedes Benz from 245–381hp meeting Tier 5 emissions standards and maximum power is available at just 1,900rpm, down from 2,000rpm.
Also, for the first time, Dynamic Power is standard. This has been available on Jaguar forage harvesters for many years, and on the Tucano it operates in a similar way to save fuel and wear and tear as power is adjusted to match demand, although operating speed remains the same. There are 10 power steps, but for unloading on the move maximum power is immediately available.
Montana versions compensate automatically for side slopes up to 16 per cent on wider body models or 18 per cent on narrower 430 and 560 variants. Final drives to the front wheels rotate hydraulically providing the height differential and an additional benefit is that both can be rotated together to provide extra table clearance for narrow gateways, allowing it to remain attached between fields.
Feeder housing adjustment up to 20 per cent allows the header to follow the ground angle while the combine remains horizontal.
Further advantages include cutting angle adjustment, allowing the table to be tilted forward to more easily pick-up laid crops by presenting the knife closer to the ground, or tilted back to reduce losses by keeping seed from over-ripe crops or oilseed rape in the header.
Hill-side models come with a 2-speed manual transmission with automatic engine load adjustment. In both gears there are 2 drive ranges, selected dependent on wheel drive loading and the speed change occurs automatically on the move maintaining traction and motion.
All-wheel drive provides up to 70 per cent more tractive power compared with standard model 4wd, through a more powerful independent hydraulic system, and a differential lock for the front axle is standard.
For further improved hill harvesting performance a 3d sieve box and auto-slope compensation by the fan are additional options, also available on standard models. Using the hill compensation system only requires the operator to select the ‘A’ button and settings are made and adjusted automatically with the actual ground angle displayed on the Cebis terminal.
“The narrow 430 is attractive to smaller farms and the new specification and availability of the Montana version will certainly add to its appeal,” said Adam.
Improved controls
The 2019 Tucano models have a new Cebis touch-screen monitor which allows performance monitoring and ease of adjustment through an intuitive screen menu. The operator has only to select the combine system to be adjusted with a tap on the image and a sub-menu opens up displaying adjustments available. Touching the relevant icon then allows the setting to be changed. Claas realises that not all operators like electronic displays so a quick-access bank of traditional switches on the new armrest allows the same range of adjustments to be made.
The Cebis screen also allows quick selection without all the menus by allowing users to set ‘favourites’ for fast recall using buttons on the CMotion joystick.
The terminal can be positioned anywhere in an arc from the user’s right knee to the right hand side. This allows it to be swung out of the way for a clear view of the full knife width, or positioned in front when constant attention to settings is preferred.
Auto Crop Flow, available previously only on Lexion models is added to the Tucano options list. Sensors measure the APS drum, residual grain separation system, straw chopper and engine and automatically react to overloading by stopping the header and intake elevator, while alerting the user. This allows operators to confidently push the combine to work at higher outputs without fear of blocking the threshing or separation systems.
Higher grain capacity
Grain tank capacity up to 11,000 litres is available on the new range, including on the largest Tucano 580 Montana, and even the smallest Tucano 320 has either 6,500 or 7,500 litres available. A further update is an automatic unloading auger flap which engages when the auger is stopped, preventing grain spillage even when the auger is still full.
For 2019 additional benefits of the latest Tucanos include;
Grain feeder housing dust extraction, improving visibility in dusty conditions and particularly at night.
Returns information displayed on the Cebis screen allowing assessment alongside grain losses.
Increased tool and spare part storage space.
Larger maintenance panels for improved service access and an on-board water tank allowing hands to be washed in the field.
Automation adds output
Cemos combine automation was launched by Claas in 2012 and precision farming product manager Edward Miller said it is now in its third generation with take-up increasing each year. “It costs extra but we have seen a strong trend for those who have had it, specifying it again when combines are updated,” he explained. Advantages include reduced working costs due to higher output and saved time, improved grain quality, better performance in the field – particularly operating in laid crops – and constant performance optimisation all day, where an operator eventually becomes tired. “It doesn’t replace an operator,” he added. “It helps those with less experience make the most of the combine’s potential and experienced operators like it as it helps them fine-tune the harvesting operation.
“Overall, when we compare combines working in all countries with Cemos against identical machines without, we see 15–18 per cent improved output.”
A new 12in high-resolution touchscreen version of the Cebis Mobile terminal is available for 700 Hybrid and 600 straw-walker models allowing easier and faster set-up and improved performance monitoring. A silhouette of the combine includes settings for the main function areas such as the rotor and fan speed, grain moisture content and grain tank fill level in progressive steps. “Accurate grain tank level information is especially useful for those using our Fleetview system for fleet management as trailer drivers are kept informed of when they will be needed,” added Edward.
Slider controls on the screen allow the operator to set the Cemos system to prioritise grain quality, straw quality or throughput.
The new Cebis Mobile terminal is also used to monitor 4D cleaning and to set up and monitor results from the grain quality camera, mounted at the elevator head. The camera records images at intervals up to one per second which are analysed to identify broken grains and foreign bodies including un-threshed heads. An image of the grain sample is displayed with damaged grains or chaff highlighted in pink and blue and by touching the screen the operator opens a second window allowing system sensitivity to be altered, for increased or decreased threshing and cleaning.
The screen also displays Cruise Pilot status. Cruise Pilot automatically adjusts operating speed up to the limit set depending on crop volume in the feeder housing, throughput in t/hr and engine load, with all parameters displayed.
Factors limiting performance are highlighted and the operating mode can be set to constant speed, constant throughput or constant throughput with losses.
Automated control
Optional Cemos Automatic comprises three modules. Cemos Auto Cleaning is available for all Lexion 600 and 700 models and a new option is Auto Threshing. Lexion 700 models can also have Cemos Auto Separation.
Auto Threshing works with Cruise Pilot and the other Cemos modules when fitted, to adjust drum speed and concave gap. Taking a basic crop setting as the start point, Auto Threshing then finds the ideal drum speed and concave setting to thresh the crop, but keeps the action as gentle as possible.
Auto Cleaning works with the grain quality camera and automatically adjusts the fan speed and upper and lower sieves constantly to maintain optimum grain quality. Four operating strategies can be set; Maximum Throughput, Optimum Fuel Consumption, High Grain Quality or a combination of all three.
Auto Separation on 700 Hybrid models automatically adjusts rotor speed and cover plates depending on the operating priority selected. Cemos Auto Separation reacts and adjusts settings constantly for optimum performance.
A demonstration of the system on a Lexion 780 proved the benefits. The sloping field of wheat appeared an even crop but from one side of the field to the other the automatic threshing system varied the drum speed and concave gap as variations in the numbers of broken grains or un-threshed heads were detected. Unless the images were inspected very closely there was little difference detectable by eye, but the combine’s system is more thorough, identifying minute variations. What is comforting for the operator is that the image quality on the high-resolution screen is clear enough to see each grain, so there is no need to constantly check the grain tank contents.
Balers updated
New model Rollant 540 fixed chamber round balers have a stronger chassis and new roller design, improving durability and improving bale formation. There are three variants, all suitable for demanding farm or contractor use, including the 540RF (Roto Feed), 540RC (Roto Cut) and 540RC (Comfort).
Bale size is 1.25m diameter and 1.22m wide made in a chamber with 15 rollers, all constructed from 4mm steel.
The 15 rollers have a modular build, with new bolted stub shafts, and a serrated profile for efficient bale gripping even in wet conditions and the Claas MaxPressure System (MPS 2) is an option, with rollers 7, 8 and 9 on a pivot mounting to apply pressure earlier in the bale forming cycle for improved density.
An improved rear door fastening system, with closing rams horizontally mounted at the sides, has been introduced to cope with the higher pressures and ensure perfect bale formation.
The rollers are driven from the left side with direct drive for uniform force distribution. Chains are 1.25in to the rotor and main drive and the tailgate rollers have a 1in chain. Bearings are upgraded over previous 374 and 375 models.
Central lubrication is an option, but for manual greasing most grease points are grouped in blocks.
The pick-up is 2.1m as before and the well-proven double crop roller is now joined by additional options of a single roller or baffle plate at reduced cost. “We have always found users get on particularly well with the double roller but where it isn’t needed the new options provide a cost-effective alternative,” explained product specialist Dean Cottey.
For bale wrapping the net system has a new brake, and the new RC Comfort model can be used with net or film wrap. Changing between the two takes under 10 minutes. “Film holds the bale shape better during handling, and gives added protection,” explained Dean. “Additional advantages are that it can be disposed of with the plastic wrap rather than having to separate the net from the film, and it also wastes less of the crop as it comes away clean rather than with material stuck to it. That is likely to be a valuable benefit this year when fodder and bedding are in short supply.”
Stronger construction includes a 80mm full width beam axle replacing previous bolt-on stub axles and a wider range of tyres as well as air or hydraulic braking.
Control is by the standard Operator terminal but options include the Communicator or full management from the tractor’s Isobus link. An iPad can also be used through a free Claas app. Settings can be altered from the cab including net delay and the drop-floor, but the Comfort specification also allows the number of net layers to be set, the net brake to be adjusted and the number of chopping knives to be selected, all from the seat.
Faster mowing
A new front-mounted Disco mower was displayed at the event. The Claas Disco Move offers superb ground contour following and mounts on an A-frame allowing rapid hitching and unhitching from the tractor or direct hitching to the tractor front link arms. For unhitching, the mower suspension is isolated using a selector lever and for re-hitching a simple pair of arrows have to be matched so that the tractor’s front linkage arms are the correct height.
The headstock is narrow allowing great forward visibility. Active Float suspension is standard, integrated within the main frame and allowing ground pressure to be adjusted to suit the conditions. The new suspension allows mower travel up and down to 1,000mm, independent of the front linkage.
The mower is pulled from the front, with low mounted arms inclined at a low angle for smooth operation. Two pre-series mowers have operated in the UK and Dean said feedback from users has been very positive, including one saying the design allowed perfect cutting even at speeds up to 20kph.
Jaguar flagship
A new flagship to the Jaguar 800-series forage harvester range has been added for next year. The 800-series was introduced 25 years ago including models from 300–500hp but the new 880 tops the 2019 line-up with 626hp from a 15.6-litre Mercedes Benz power unit.
Dean Cottey said the new model provides an alternative for those needing high capacity and has the same engine as the Jaguar 960 but will suit those who don’t want to move up to the physically larger 900-series.
The new model is ideally suited to livestock farms and contractors producing silage for livestock feed with a chop length of 9–10mm and longer.
Three pre-series models have operated for the 2017 and 2018 seasons having replaced previous 492 and 496 models, and harvesting grass, wholecrop and maize. Dean said they have performed well against previous models.